Air Caster Tech in the Shipyard
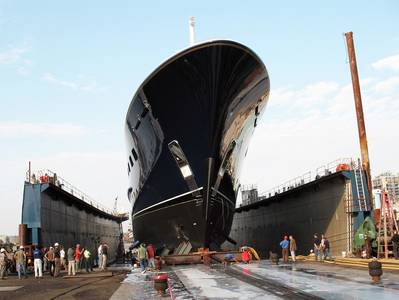
The megayacht Cakewalk, built at Derecktor Shipyards’, Bridgeport, Ct., shipyard was launched using air bearings. Photo courtesy AeroGo, Inc.
Like the magic carpet of ancient myth, air caster technology has revolutionized the way in which heavy payloads can be moved in a cost effective and efficient way — floating on air. Developed post-World War II by engineers at General Motors, air casters were later modified and improved for the construction of the iconic Boeing 707 in the early 1960s. Today, used in a host of industries, companies in the maritime industry are employing air casters to handle lifts from mega-yachts to massive hull sections and Z-drives.
A Primer
A form of hydraulics that uses air instead of fluid, air casters rely on torus bags that expand as they are filled with compressed air. As they reach their inflation limit, air begins a controlled escape and is released in a steady even flow that creates a seal with the floor and carpet of air on which the load floats similar to an air hockey puck.
The floating nature of air casters provides friction-free, omni-directional movement, which means heavy loads can be transported freely in any direction almost literally, with the push of a finger—a virtually impossible task for conventional cranes, rollers, rails, or skid beams.
These capabilities meld to provide a unique system capable of moving vessels and major components during construction and repairs or for loads from 1,000 pounds to as much as 6,000 tons.
Practical examples
For example, Z-drives, installed vertically into a ship’s hull, can be challenging to install. Air caster technology allows the drive to be slid onto the vessel and then winched up into position with a precision fit. The same holds true of propeller installation, where the fit of the hub to the shaft must be exact. This is where the omni-directionality, as well as the precision lift capability of air caster systems, comes into play. The freedom of movement of the air casters provides for the precise positioning of an otherwise awkward vessel component.
Air caster technology is used extensively in Korea, moving massive hull sections where hull components are moved from where they’re fabricated for positioning on the vessel’s framework. Once in position, small, lightweight guides on the hull are used to pilot the precise marriage of the new section with the hull.
Going where no crane can go: air bearings move the skid to install the prop. Photo courtesy AeroGo, Inc.
In July 1989, the technology was used by the National Shipbuilding & Drydock Company in San Diego, Calif., to repair the Exxon Valdez. The VLCC had sustained serious damage and required extensive work on its buckled bow. With the ship resting in a drydock, the yard turned to AeroGo technology to precisely lift a quarter-inch thick, 200-plus ton, 30 x 80-ft. hull plate under the hull and exactly align it with the ship’s repaired frames.
In 2010, the largest and heaviest transformer in the world—a 700-ton, one million KVA/2000KV test reference transformer—was moved in Chanzhou, China utilizing AeroGo’s air caster technology. The unit was moved via a sophisticated computer control system to synchronize the movement of two smaller transporters which together reach the total capacity of 800 tons.
More recently, Derecktor Shipyards’ Bridgeport, Connecticut, needed to move a 3,200 ton mega-yacht from the structure in which it was built, down a slipway and a 30-degree left turn to line up with the drydock. Implementation of an air caster system reduced not only the time needed to build the vessel, but provided the yard with the flexibility of handling larger craft and moving them from weather shelter, down the slipway and out onto the drydock and launch it.
The cost to the yard for the air caster system was $500,000 and required virtually no time to install. That, compared to the $4 to $6 million that would have been needed to build a conventional rail system and taken at least a year to install. Should the yard ever decide to relocate or expand its operations, unlike a conventional rail system, the air caster system can relocate with them.
On-board, air caster technology is currently used to move generators, pumps and other heavy equipment, while air caster pallets are used on Trident submarines to float 1,500 lb. pallets of stores for storage between the missile bays. Limited space handled with zero friction so the pallets can be fit into the tightest space with a single crew member can move a 1,500 pallet with ease.
About the Author
Randy Manus is a Senior Application Specialist with AeroGo, Inc., in Seattle, Wash. AeroGo manufactures heavy load equipment utilizing hovercraft technology for moving heavy, awkward or delicate loads.